Products
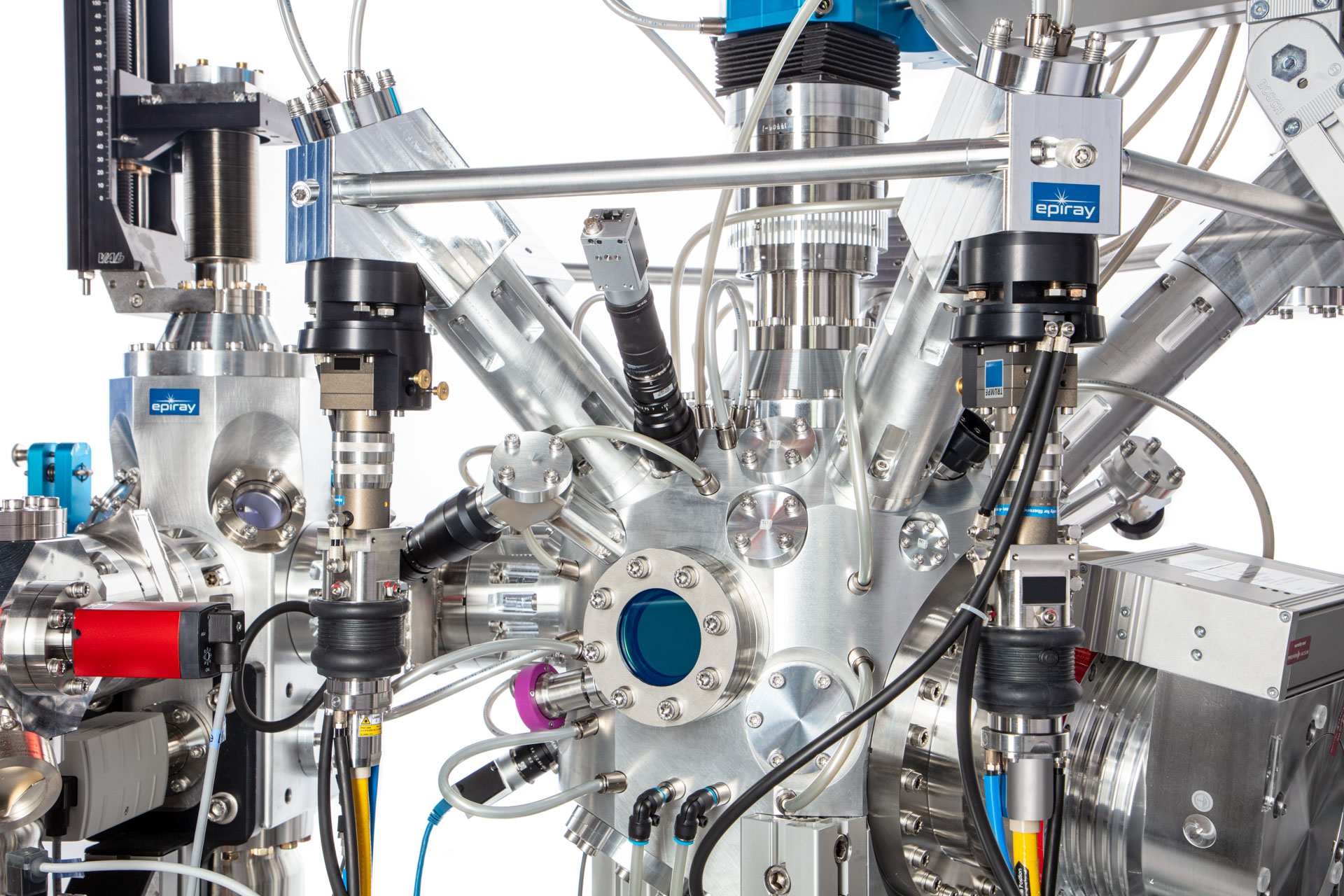
STRATOLAS
Thermal laser epitaxy
STRATOLAS is a complete epitaxy system that is specifically designed and optimized for TLE. This allows for a small chamber design with a minimum number of parts inside the vacuum space. The system is equipped with our CO2 laser substrate heater and can handle up to 5 different elemental sources.
Unique features
- Universal compatibility across the entire periodic table on every source position
- Local source heating for ultrapure epitaxy
- THERMALAS substrate heating up to >2000 ℃
- Broad compatibility with process gasses (O3, O2, N2, NH3) up to 10-2 mbar
- Rapid source material exchange without breaking the vacuum
Control and throughput
- Real time process monitoring with RHEED
- Small and fast loadlock, UHV storage
Class 1 laser safety
- Class 1 qualification: hermetically sealed system, integrated water cooling and safety interlocks
- Process monitoring using cameras
Substrate size
STRATOLAS 5: 5 by 5 mm2
STRATOLAS 10: 10 by 10 mm2
STRATOLAS 25: 1-inch diameter
STRATOLAS 50: 2-inch diameter
STRATOLAS 100: 4-inch diameter
Additional options
- Between 1 and 6 source heating lasers
- Connection to existing vacuum clusters
- User-specific configuration for shutters, RHEED, additional storage space, etc. available on request
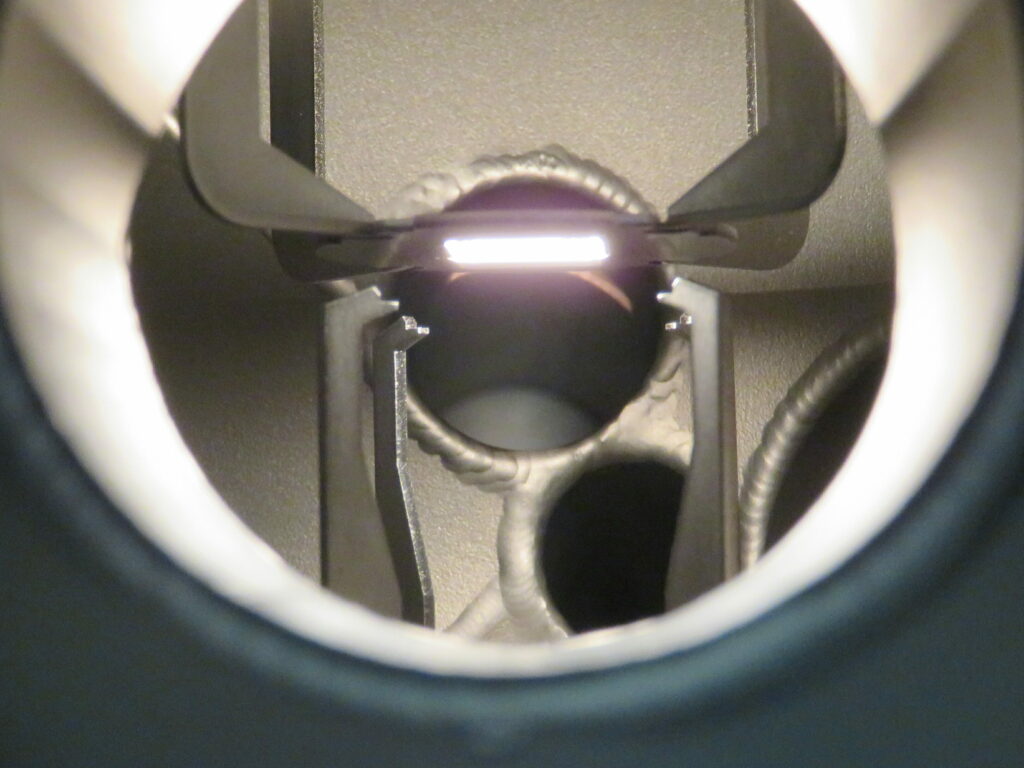
THERMALAS
Laser substrate heating
With THERMALAS, substrate heating takes minutes instead of hours. It gives you higher temperatures and faster ramp up/down rates. For low temperatures, it’s better than others. For high temperature, it’s the only choice.
You can use our THERMALAS substrate heater to upgrade your existing PLD or Sputter vacuum chamber. And you can use it later as a core component for our STRATOLAS TLE system.
Overview
Laser heating enables high substrate temperatures in an ultraclean environment. Our solution ensures light is absorbed well by all common substrate materials. It also minimizes contamination of the substrates, e.g. from glues or metal contacts.
Furthermore, extremely high temperatures and fast ramp rates are possible because only the substrate is heated. The substrate holder always remains much colder than the substrate because the absorption of our laser light by metals is small. The figure above shows an example of a sapphire crystal at T = 1700 ℃.
Access to higher temperatures allows for rapid thermal preparation of well-defined oxide surfaces in situ prior to growth, obviating the need for arduous chemical etching and improving throughput.
Ultimate performance
- Access substrate temperatures up to >2000 ℃ and ramp rates up to 400 ℃/s
- Tight PID control with an on-axis pyrometer over a dynamic range of more than 3 orders of magnitude
- Local heating minimizes outgassing
- Thermal preparation of terminated, growth-ready surfaces in minutes
Easy upgrade path
- Available as add-on upgrade for existing epitaxy systems
- Substrate sizes from 5x5 mm2 up to 100 mm
- Hermetically closed laser beamline and interlock for Class 1 safety rating
LINEAR SHUTTER
- 10.000.000 cycles.
- 10-10 mbar during operation.
- 50 – 200 mm travel distance.
- Compact design.
- Pneumatic or electric actuation.
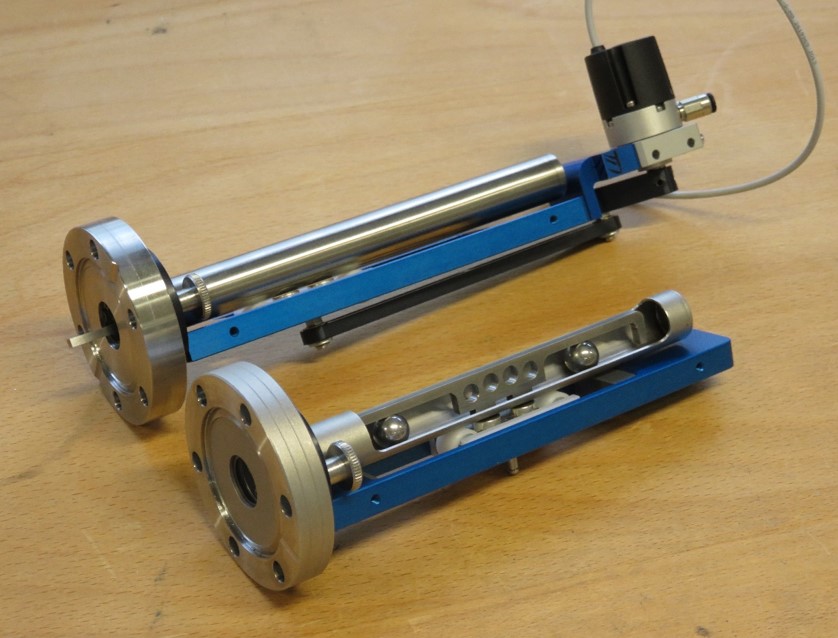