Technology
Thermal Laser Epitaxy
Thermal laser epitaxy is a physical vapor deposition technique. It uses single element sources that are heated by lasers beams in order to thermally evaporate the source material. Because the laser beams can be made with almost arbitrary power density, extremely high temperatures are possible. This allows for the evaporation of practically all elements of the periodic table with the same setup. Therefore, TLE is a very versatile deposition technique.
The chamber requires only simple holders for the sources and substrates, because the energy sources are placed outside the vacuum chamber. This benefits system simplicity and sample purity. Moreover, the direct local heating of targets in TLE ensures that only the evaporating surfaces are heated. This minimizes contamination. TLE is compatible with a range of background gasses up to pressures of 10-2 mbar.
In summary, TLE is a highly flexible deposition technique that can be used to grow almost any material with ultrahigh purity.
TLE is especially interesting for materials science in the fields of quantum computing, strongly correlated electron systems, novel material synthesis, topological materials, and energy research.
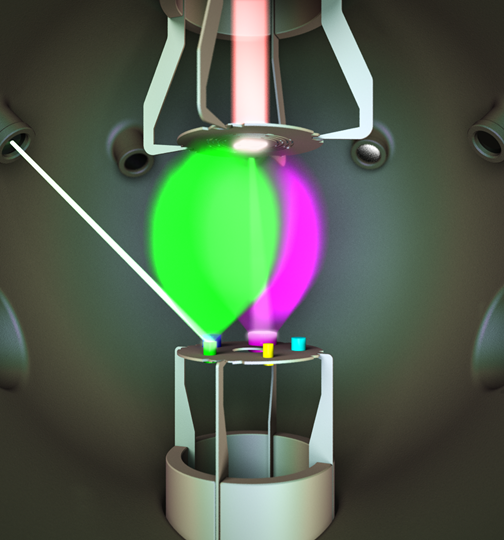
Advantages and challenges of TLE
Main advantages
- Epitaxy with almost all elements
- Ultrahigh purity
- In situ source and sample transfer
- High throughput due to high ramp rates
- Compatibility with highly reactive atmospheres
- Low operating costs
Technical challenges
TLE has some intrinsic challenges as well. Based on our long experience with TLE setup we have developed patent-protected solutions for:
- Growth stability
- Uniform melting of the sources
- Entrance window protection
- Combining sources with high and low temperatures
TLE compared to traditional technologies
Main benefits compared to:
Molecular Beam Epitaxy
- Evaporation of almost all elements of the periodic table
- Sources can be quickly transferred in & out of the growth chamber
- Efficient heating: only the evaporation spot is hot
- Fast ramping up and down of the source temperature
Main benefits compared to:
Sputtering
- High-purity single-element sources
- Elemental fluxes controlled individually
- Thermal deposition
- Sources can be quickly transferred in & out of the growth chamber
Main benefits compared to:
Pulsed Laser Deposition
- High-purity single-element sources
- Elemental fluxes controlled individually
- Thermal deposition
- No ablation particles
Direct laser substrate heating
Conventional substrate heating techniques, such as resistive heating, filament heating, quartz lamp heating and infrared laser heating, limit the available substrate temperatures to approximately 1000 °C. Furthermore, the substrate heating is indirect so that the substrate is always in contact with contaminants such as backside coatings, metal blocks or glues.
The solution to these issues is direct laser substrate heating using a CO2 laser. The far-infrared light from the CO2 laser is well absorbed by almost all oxide substrates and therefore no intermediate heat transfer material is required. Thus only the substrate itself is heated to high temperatures. This allows for epitaxy at temperatures up to the melting points of the substrates in an ultrapure environment.
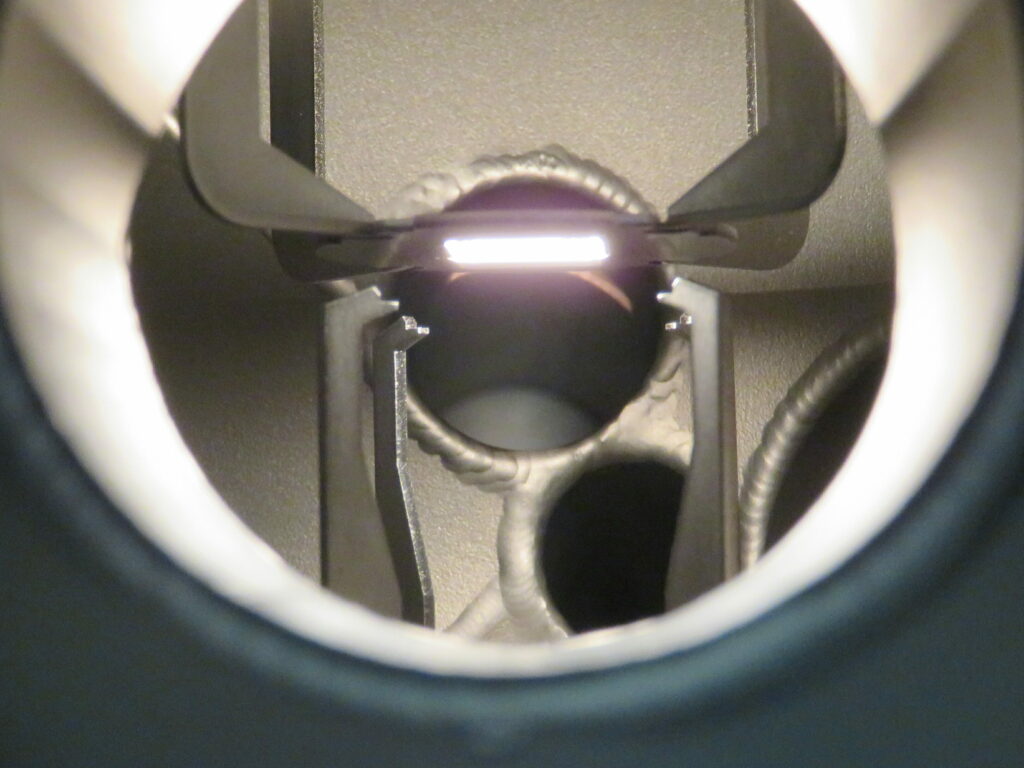
Advantages and challenges of direct laser substrate heating
Main advantages
- Temperatures up to 2800 °C
- Ultrahigh purity
- High throughput due to high ramp rates
- Compatibility with highly reactive atmospheres
Technical challenges
Direct laser heating has some intrinsic challenges as well. Based on our long experience with CO2 laser heating we have developed patent-protected solutions for:
- Substrate homogeneity
- Accurate temperature measurement
- Temperature control
- Laser safety